Damage Prevention Starts with You
The damage prevention division at NIPSCO has many moving parts. Each stakeholder, including you, plays an important role in making the 811 process work effectively. If everyone involved works to make their area of responsibility more efficient, the entire 811 system will be able to function like a well-oiled machine.
Pre-checklist:
If you can check all the boxes, you are ready for the 811 system to work without a hitch!
- Have gathered Quality Information
- Have Specifics About Dig Site Location & Dimensions
- Have Good Contact Name & Phone Number
- Have Accurate Description of Work Being Performed
- Have a handle on Ticket Quantity
- Are Providing Sufficient Notice & Eliminating Any Unnecessary Requests
- A Plan to Remove Completed Requests
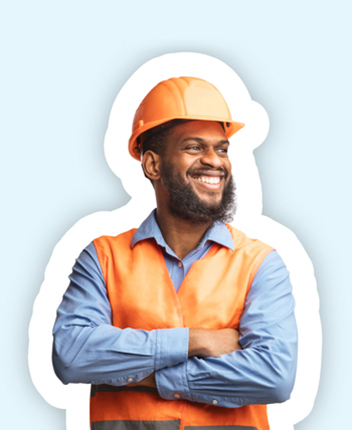
NIPSCO strives to be a dependable partner to have you be safer and more efficient every day.
Damage prevention is critical to protecting facilities, employees and customers. The well-being of the people and the communities we serve is of the utmost importance.Ways to help us work safely and proficient together!
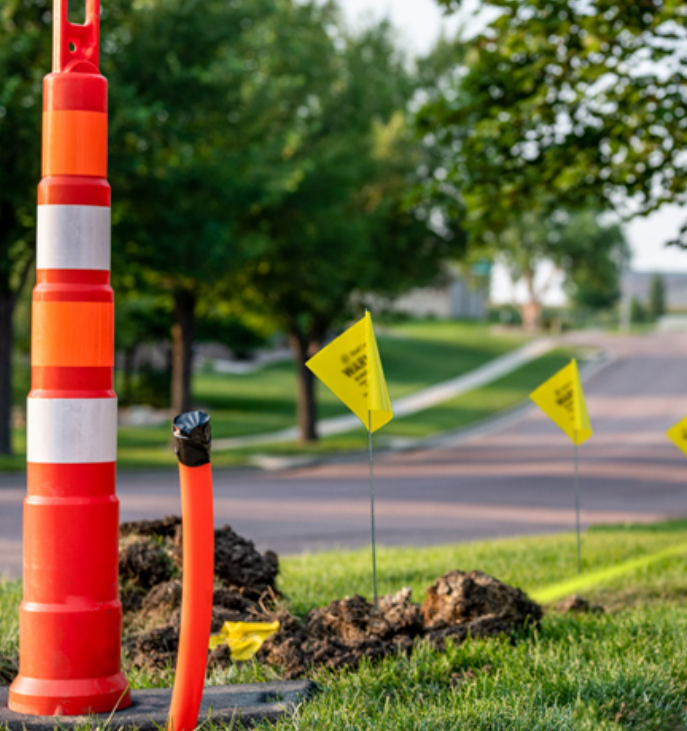
How Can You Help?
MANAGE TICKET QUANTITY
In addition to improving the quality of information you provide, we also ask that you manage the quantity of your requests.
SUFFICIENT NOTICE & ELIMINATE UNNECESSARY REQUESTS
- It’s important that you request utility locates with sufficient notice to be marked, but not more than you can reasonably begin within the life of the ticket.
- Too many tickets at once can put a strain on the system and keep locators from getting to more time-sensitive sites. So, avoid requesting "backup" sites to be marked, or creating "just in case" tickets.
- Active tickets should match the actual schedule of the work being performed and follow the requirements in your state dig law.
REMOVE COMPLETED REQUESTS
- Avoid locate renewals and remarks on jobs that have been completed.
- Often locate requests are updated or refreshed long after work has been finished.
- This causes locators to spend time marking inactive job sites when they could be marking active ones.
PROVIDE QUALITY INFORMATION
First, provide accurate and detailed information on when starting a ticket.
ACCURATE DESCRIPTION OF WORK BEING PERFORMED
- Make sure to provide an accurate description of the work being performed.
- Providing more detail enables locators to address internal concerns in advance, arrive better prepared, and get straight to business.
SPECIFICS ABOUT DIG SITE LOCATION & DIMENSIONS
- Be specific about the dig site and only request marks in the exact area where excavation work is taking place.
- Provide GPS coordinates, white-line the proposed site, and identify any relevant landmarks.
- This critical information helps narrow down the scope of work so locators can focus on marking what's really needed for each project and avoid spending time on unnecessary marks.
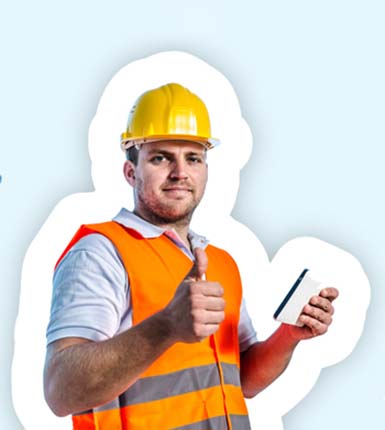
Horizontal Directional Drilling Best Practices
Before any drilling occurs, a contractor must use the state's utility location system. At NIPSCO, we want to work together to make sure we keep you and our communities safe.Below are some best practices for HDD:
Best Practices
Avoid Underground Utility Lines
Always verify underground lines, using surface markings, before drilling
vertically or horizontally to avoid hitting them. Since underground lines can
be difficult to identify if they are covered by other lines, are undocumented,
are buried at depths different from code requirements, or are in a different
position from initial installation due to ground settling, it is important to use
multiple identification and verification methods before drilling.
To verify and avoid underground utility lines when using HDD:
- Visually inspect the entire planned digging path for structures that
indicate potential underground utilities (e.g., gas meters and
manhole covers). - Review drawings and contact utility companies directly, whenever
possible, to verify underground utility locations. - Compare findings with surface markings (discussed below) to
identify any missed utility. - Employ potholing and other safety precautions described below to
further identify and avoid lines in the drill path.
One common industry practice is to call 811, the "Call Before You Dig" number, to establish the location of the of any underground utility installations in the work area.
The risk of striking underground natural gas or electric utility lines increases when HDD is used in urban areas.
Underground service locators typically cannot provide depth information for utility lines. Employers must implement safe work practices that always verify the depth of utility lines near the planned drill path to prevent hitting them.
Use Potholing to Verify Utility Lines Before Drilling
If possible, physically verify underground utility line locations by potholing along the planned drill path. Potholes are vertical holes dug by hand or with a vacuum excavator. It is important that potholes go to the planned drill path's depth—even if this is beyond the deepest known utility line—to identify any hidden lines. Potholing also allows the tracker to visually observe the drill stem and drill head during drilling to ensure that the HDD machine operator avoids striking utility lines along the drill path. The tracker typically uses a tracking device to determine whether the drill stem and head are following the planned drill path. The tracker is there to warn the HDD machine operator about utility lines with enough time to change direction if needed.
Verify underground utility lines visually by potholing. This allows the tracker to guide the HDD machine operator to maneuver the drill stem to avoid striking utility lines and prevent an incident that could result in worker injuries or fatalities
Safety Precautions to Avoid Underground Utilities
Conduct site-specific safety assessments, develop and implement site-specific work plans, train workers, and provide and ensure the use of the right equipment to workers, including personal protective equipment (29 CFR Part 1926 Subpart E). Ensure the use of safe work practices from the planning phase to completion. Potential hazards associated with HDD operations include mechanical rotating parts (e.g., struck-by, caught-in), high-pressure drilling fluid, and damaging electric and gas lines and other underground utilities (e.g., electrocution, fires, explosions). Take the following safety precautions:
- Use site-specific safety assessments to determine appropriate drilling techniques and safety practices (e.g., when potholing, drilling the bore, or using a back reamer).
- Contact the local utility location service to mark lines and assist with determining utility locations. Compare drawings with surface markings, as some utility lines may miss detection or may be missing from utilities maps.
- Review drawings and contact utility companies directly, whenever possible, to verify underground utility locations.
- Ensure that the HDD machine operator and tracker walk through the planned drill path during planning and site preparation. Check for structures (e.g., gas meters and manhole covers) that may indicate an underground utility line, obstructions along the drill path, and potential sources of interference that could affect tracking device readings.
- Use safe and appropriate potholing techniques to the planned drill path's depth to expose any hidden underground utilities.
- Train HDD machine operators and trackers before starting the operation to communicate effectively with hand signals and radios.
- Ensure trackers check the tracking device readings frequently during HDD operations and compare them with the pre-operational walkthrough readings. If any changes in readings occur (e.g., depth), the tracker should immediately signal the HDD machine operator to stop drilling, investigate, and take appropriate safety precautions before continuing to drill.
- Instruct trackers to look into the potholes to observe the:
- drill stem as it passes near underground utility lines during drilling, and guide the HDD machine operator along the bore path to avoid striking a line;
- back reamer to verify that it follows the bore path and avoids utility lines. - Drill at a pace that is slow enough to permit the tracking device to sense any drill line deflections caused by large obstructions.
How Striking a Natural Gas Line Can Result in an Explosion and Fire
Striking underground natural gas lines may present explosion and fire hazards in the workplace and surrounding areas. If the drill stem, drill head, or back reamer strikes a natural gas line, gas may leak into the workspace, or build up where air can get trapped in the area (e.g., buildings, vaults, pits), and result in an explosion and fire. Natural gas is easily ignited by an open flame, static electricity, glow plugs from diesel engines, or sparks from the HDD machine or nearby equipment. As natural gas accumulates in a space, higher concentrations increase the risk for an explosion and fire.
Prevent or Minimize the Impact of Natural Gas Explosions and Fires
Employers must develop a fire protection program and follow it throughout all construction phases, including HDD operations (29 CFR Part 1926 Subpart F). Employers must prohibit open flames and smoking at a worksite when conducting HDD operations (29 CFR 1926.151(a)(3)). Develop and implement an adequate site-specific Emergency Action Plan (EAP) for workers to follow for different emergencies that could occur—such as gas, electric, or sewer line strikes—and communicate the plan to all workers (see 29 CFR 1926.35(e)(2) for OSHA requirements related to EAPs in construction). Include steps in the EAP to take if a natural gas leak is suspected, including immediately evacuating the area and, from a safe location, calling 911, and the utility company. If using a cell phone, move away from the area where there might be gas before calling. Employers need to train all workers on appropriate precautions to take during different emergencies, immediately alert all workers in an emergency, and evacuate workers from unsafe areas to a safe, predesignated assembly location.
How to Identify a Natural Gas Leak
Employers must ensure that workers can identify a potential natural gas leak. Handheld natural gas detectors are most effective, but other indicators include:
- Dirt, water, or debris blowing from the ground into the air.
- An unusual sound, such as hissing, whistling, or roaring, near a natural gas line.
- Smelling a distinctive sulfur-like odor, which is typically added to natural gas, although some people cannot smell the odor. Note that not all gas is odorized, especially at large industrial sites, and may be impossible to smell.
Immediately contact local emergency responders (e.g., call 911) if excavation damage results in a natural gas release. See OSHA SHIB Hazards Associated with Striking Underground Gas Lines
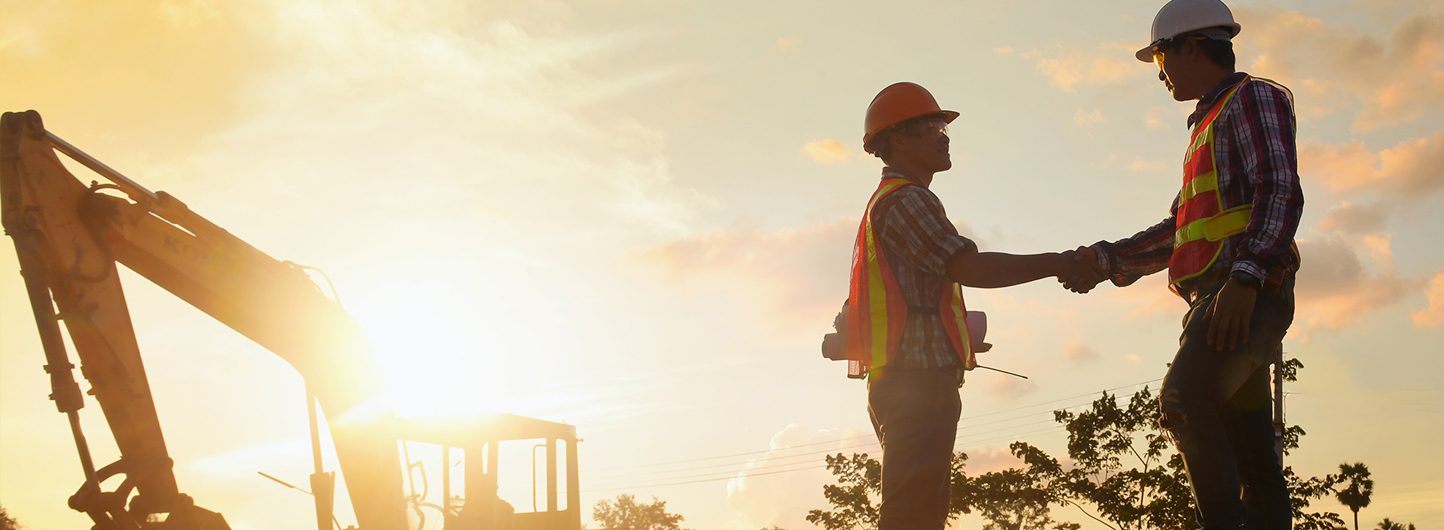
Looking for more resources?
- Damage Prevention Coordinators
- Excavator's Fact Sheet Color Codes for Utilities
- Tolerance Zones
- Tips and much more